Report of a Visiting Scholar at Tokyo College Part 1 – Masters of the Grain: A Journey through the World of Japanese Woodworking
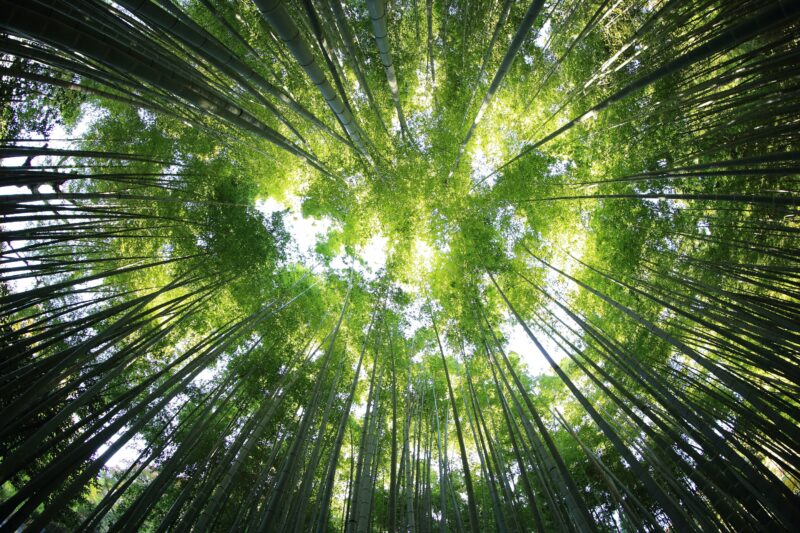
Lianara Patricia DREYER(Visiting Scholar, Tokyo College)
In this blog post, I am pleased to share my experiences as a Visiting Scholar at Tokyo College. In Germany, I work at the Berlin Social Science Center (WZB) where my focus is on crafts, more precisely the use of digital technologies in the craft sector. Craftmanship includes, for example, bakers as well as carpenters. One of the crafts that I am more deeply involved with is woodworking. Although a lot of the work is generally carried out with machines in German woodworking companies, during my field work in Japan woodworkers repeatedly emphasized how central the feeling of wood is to them.
This feeling, which not only means an ability to work with wood but also dedication, adequate handling, and a certain work ethic, is one reason that brought me to Japan. As a country of forests, with two thirds of the land covered by forests (Forestry Agency 2022), Japan has a long tradition of woodworking. Numerous temples and shrines for which it is known worldwide bear evidence to its exceptional status. The most impressive example for me is the Hōryū-ji Temple in Ikaruga that contains the oldest wooden buildings in the world (Cultural Resource Utilization Division, Culture, Education and Creative Living Department 2022). These temples were built by the Miya-daiku, the shrine and temple carpenters (Mertz 2020; Miller 2016), who represent one group of Japanese woodworkers. Apart from them, there are also the Sukiya-Daiku, the teahouse and residential carpenters, and the Tategu-shi-Interior finish carpenters who are known for making Shoji. The fourth group is the Sashimono-Shi, the cabinet and furniture makers (Miller 2016), who are famous for connecting wood pieces without using nails (Tokyo Metropolitan Government 2023), a technique that immediately fascinated me. Sashimono-Shi have shaped different styles and eras. The Edo Sashimono style developed from the 17th to 19th century (ibid.) with typical works such as furniture for samurai and wealthy merchants and dressing rooms of Kabuki actors (ibid.). The Edo Sashimono style, developed in the Tokyo region, was designated as Traditional Crafts of Tokyo by the Government of Tokyo (ibid.). It was this historical background of traditional woodworking that led me to conduct field research in Japan.
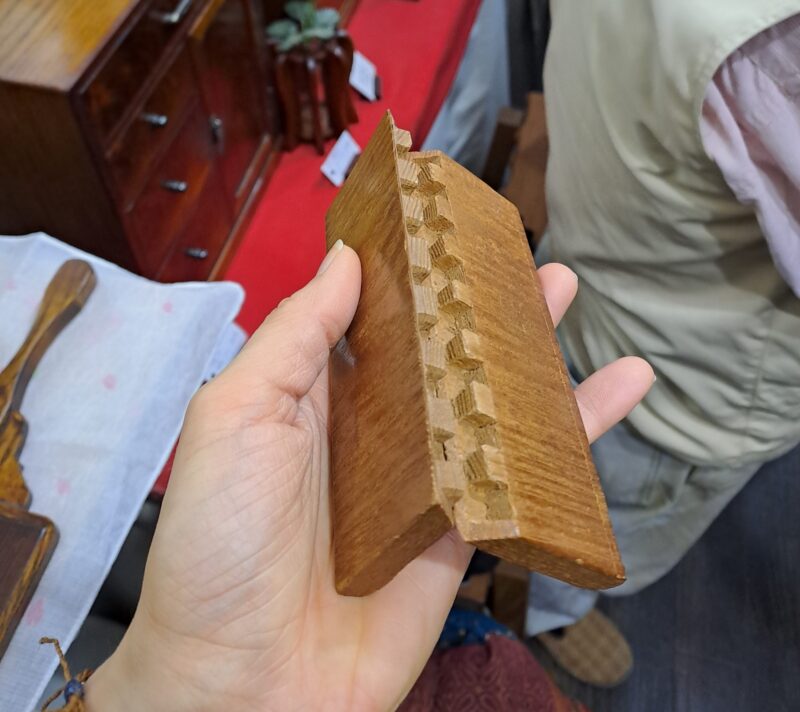
Picture 1: Connected without the use of nails
While conducting research in Japan, I investigated how traditional woodworking is developing today by interviewing experts and visiting woodworking workshops. My starting point was that woodworking is facing challenges: changing lifestyles and consumption patterns of the population have led to a declining demand for wood products. The woodworkers I visited choose different strategies to deal with this challenge.
Some of the businesses still practice sashimono today. The sashimono woodworker Yutaka Mogami is a good example (Kogei 2018). As buying large pieces has become unusual today, the sashimono master has adapted to the changing demand and is now increasingly producing everyday items, such as accessories and kitchen utensils in the sashimono style (Kogei 2024). Necessity is paired here with the preservation of tradition. Chisels are used to make the wooden joints, while the surface treatment is carried out with Japanese hand planes, the kanna. The concept of sashimono everyday items has potential to continue as the master’s son has agreed to take over the business.
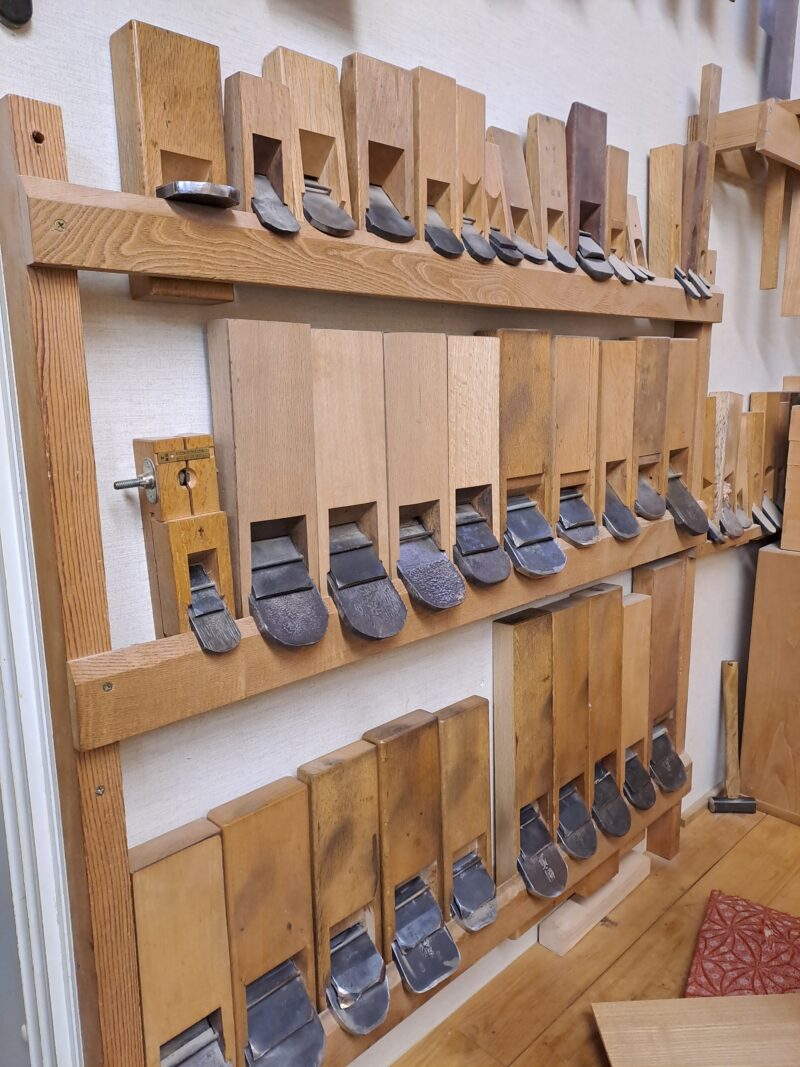
Picture 2: Japanese hand planes “Kanna”
Other woodworkers combine traditional production techniques with the use of manual machines. Their focus is on the product design, while preserving traditions plays a minor role. These woodworkers are also trying out new production methods. A notable example is the Studio Jig by Kenta Hirai (Studio Jig 2024). This woodworker has developed the free from lamination technique, which is used to shape the wood of the Yoshino cedar into round forms (Studio Jig 2017). Thereby, the particularly soft material is strengthened so that it is suitable for furniture production. Hirai explains: "I wanted to create something that makes people think about the concept of furniture as well as the concept of unused wood" (Studio Jig 2024). Through his innovative work, he shows that with the appropriate technique, Yoshino cedar can indeed be used for furniture making.
Picture 3: Kenta Hirai in his workshop with a chair made with the “free from lamination”-technique
The woodworker Asakura Mokkou also works for the further development of traditional products within his workshop (Mokkou 2024). Instead of limiting himself to traditional sashimono products, his company produces tables, chairs and cabinets. The woodworker carpenter has even set up a second workshop particularly to produce large objects. During the production process, manual machines are used for the rough processing steps of the wood. The finishing touches, i.e. the surface treatment, are then carried out using kanna. The woodworker sees his work as follows: "At first, I studied traditional crafts at the university. After graduation, I learned woodworking and modern design in a company. Currently, I am running my studio in a style, which is a mix of the two. So, it is a connection of traditional craft with modern design." This production method requires more working time than using machine technology alone, which means that the joinery's products are also more expensive. However, Mokkou's customers are willing to pay this price due to the longevity of the furniture. For Mokkou's work, this means: "That's the reason why a long-life design is necessary, a timeless design. There is not one important point, for example the material. The design, ease of use, the material feels durable and unbreakable, ease of repair. I think about total balance."
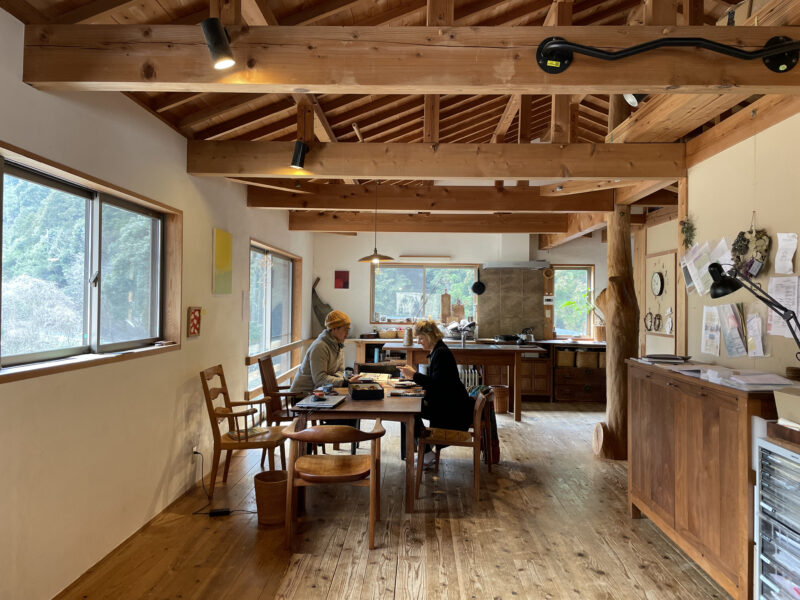
Picture 4: Interview with the woodworker Asakura Mokkou
In addition to innovation, the preservation of traditional Japanese carpentry craftsmanship and the passing on of knowledge are also of great importance. One instance I have seen is Mount Fuji Wood Culture Society. The non-profit organization was founded in March 2020 (Mt. Fuji Wood Culture Society 2024). Its founder, Tak Yoshino, learned his craft from sashimono masters and therefore sees his work with wood as directly connected to the forest. With the support of his family and a small team, he set up a workshop on a forest site. Craft courses lasting one to several weeks are held there, also for foreigners who want to learn the basics of Japanese joineries and tools. In order to preserve the traditions of sashimono, knowledge is not only taught in courses, but also through in-house training, where apprentices live with the master's family and are introduced to the use of the tools in the workshop. The master craftsman pursues a clear strategy: Mastering the most difficult tool, the kanna, comes first, as it makes all remaining activities easier.
The different companies and woodworkers are examples of how woodworking is developing in Japan. My field visits have revealed that traditions are being preserved, but fundamental changes are also taking place through product innovation and the addition of manual machines. Even if not all of the businesses mentioned fit into traditional wood craft or are classified as such, the businesses are still connected through the origin of their production methods—the use of traditional tools and the connection to wood as part of everyday life, i.e. is a fundamental feeling for wood.
References
Mokkou, Asakura. Fieldnotes of the company visit. 2024.
Cultural Resource Utilization Division, Culture, Education and Creative Living Department of Nara Prefecture. Nara Prefecture. World Heritage Journal. 2022. https://www.pref.nara.jp/secure/253850/WHJ03en_web.pdf.
Forestry Agency of the Ministry of Agriculture, Forestry and Fisheries. Annual Report on Forest and Forestry in Japan. Fiscal Year 2022. 2022.
Mertz, Mechthild. Japanese Wood and Carpentry. Rustic and Refined. Kaiseisha Press. Otsu City. 2020. https://www.kaiseisha-press.ne.jp/img/9784860993672pr.pdf.
Kogei, Mogami. Fieldnotes of the company visit. 2024.
Kogei, Mogami. Website of the Sashimono association. 2018. http://sasimono.ciao.jp/English/about_Mogami/founding.html (last accessed: 1.05.2024).
Miller, Hugh. Japanese Wood Craftsmanship. 2016. https://www.hughmillerfurniture.co.uk/wp-content/uploads/2016/04/WCMT-Report-Final-Online-v2.6-Spreads-Smallest-File-Size.pdf.
Mt. Fuji Wood Culture Society. Fieldnotes of the company visit. 2024.
Studio Jig. Fieldnotes of the company visit. 2024.
Studio Jig. Website of the company. 2017. https://www.studiojig.com/ (last accessed 2.05.2024).
Tokyo Metropolitan Government. Traditional Crafts of Tokyo. Edition (4)111. 2023. https://www.dento-tokyo.metro.tokyo.lg.jp/pdf/202307_en.pdf.